1
/
of
1
SEDAYUBET: Situs Daftar Judi Bola Online Agen Sbobet Mix Parlay Sbobet88 Betting
SEDAYUBET: Situs Daftar Judi Bola Online Agen Sbobet Mix Parlay Sbobet88 Betting
Regular price
Rp 8.888.888,00 IDR
Regular price
Sale price
Rp 8.888.888,00 IDR
Unit price
/
per
SEDAYUBET adalah situs daftar taruhan judi bola online permainan agen sbobet mix parlay betting di sbobet88 resmi link alternatif dan login mobile apk sbotop auto slot gacor terpercaya.
Share
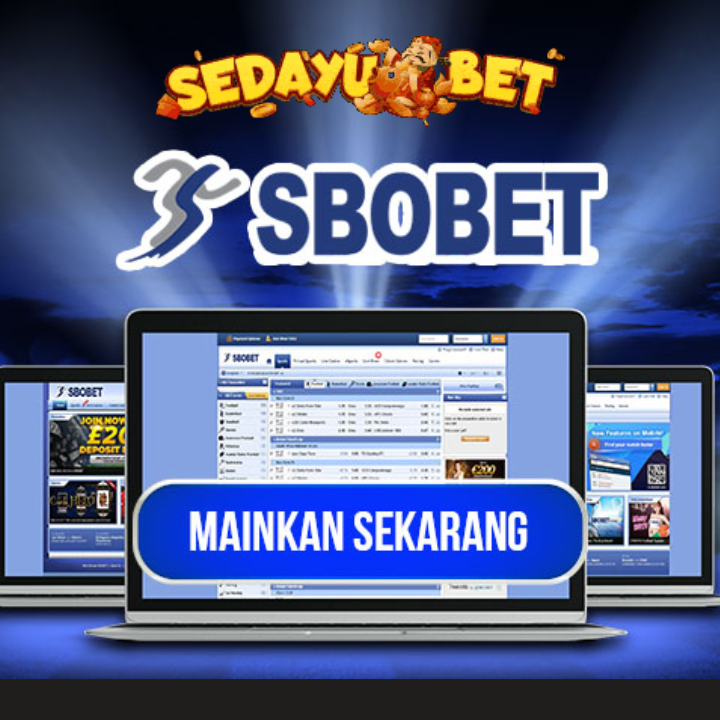